Steel, a fundamental material in various industries, undergoes intricate processes to enhance its properties. One such grade that stands out is S355JR. In this post, we delve into the depths of S355JR heat treatment, exploring its significance, processes, and the transformative impact it has on the mechanical properties of this exceptional steel.
Understanding S355JR: A Brief Overview
Before delving into the nuances of heat treatment, let’s acquaint ourselves with S355JR. This structural steel boasts a minimum yield strength of 355 MPa, making it a preferred choice in construction and engineering projects. Its versatility and robustness make it a cornerstone in building structures that endure the test of time.
The Essence of Heat Treatment
Heat treatment is a pivotal step in the manufacturing process of S355JR, playing a crucial role in determining its mechanical properties. This controlled heating and cooling process aim to alter the steel’s microstructure, enhancing its strength, hardness, and other essential characteristics.
The Stages of Heat Treatment
1. Annealing:
In the initial phase, S355JR undergoes annealing, a process where the steel is heated to a specific temperature and then gradually cooled. This promotes internal stress relief and refines the steel’s grain structure.
2. Normalizing:
Normalizing follows, involving heating the steel to a temperature above its critical range and then allowing it to cool in air. This process imparts uniformity to the steel’s microstructure, enhancing its mechanical properties.
3. Quenching and Tempering:
Quenching involves rapid cooling of the steel, increasing its hardness. Subsequent tempering imparts toughness and ductility, striking a balance between hardness and strength.
Advantages of S355JR Heat Treatment
The meticulous heat treatment of S355JR bestows numerous advantages upon this steel grade:
- Increased Strength: The process enhances the steel’s yield and tensile strength, crucial for withstanding varying mechanical loads.
- Improved Toughness: Through tempering, the steel attains a fine balance between hardness and toughness, ensuring resilience in real-world applications.
- Enhanced Wear Resistance: Heat treatment augments the wear resistance of S355JR, extending its service life in demanding conditions.
Common Applications of Heat-Treated S355JR
S355JR, after undergoing the transformative heat treatment, finds its application in:
- Structural Engineering
- Construction of Bridges
- Manufacturing of Heavy Machinery
- Offshore Structures
Conclusion
In conclusion, S355JR heat treatment is a meticulous process that elevates the properties of this already exceptional steel grade. The controlled application of heat and subsequent cooling stages endows S355JR with strength, toughness, and durability, making it an indispensable material in diverse industrial applications.
If you have further questions or specific requirements related to S355JR steel, feel free to reach out to us via email at sharon@otaisteel.com or through WhatsApp at +8613580960968.
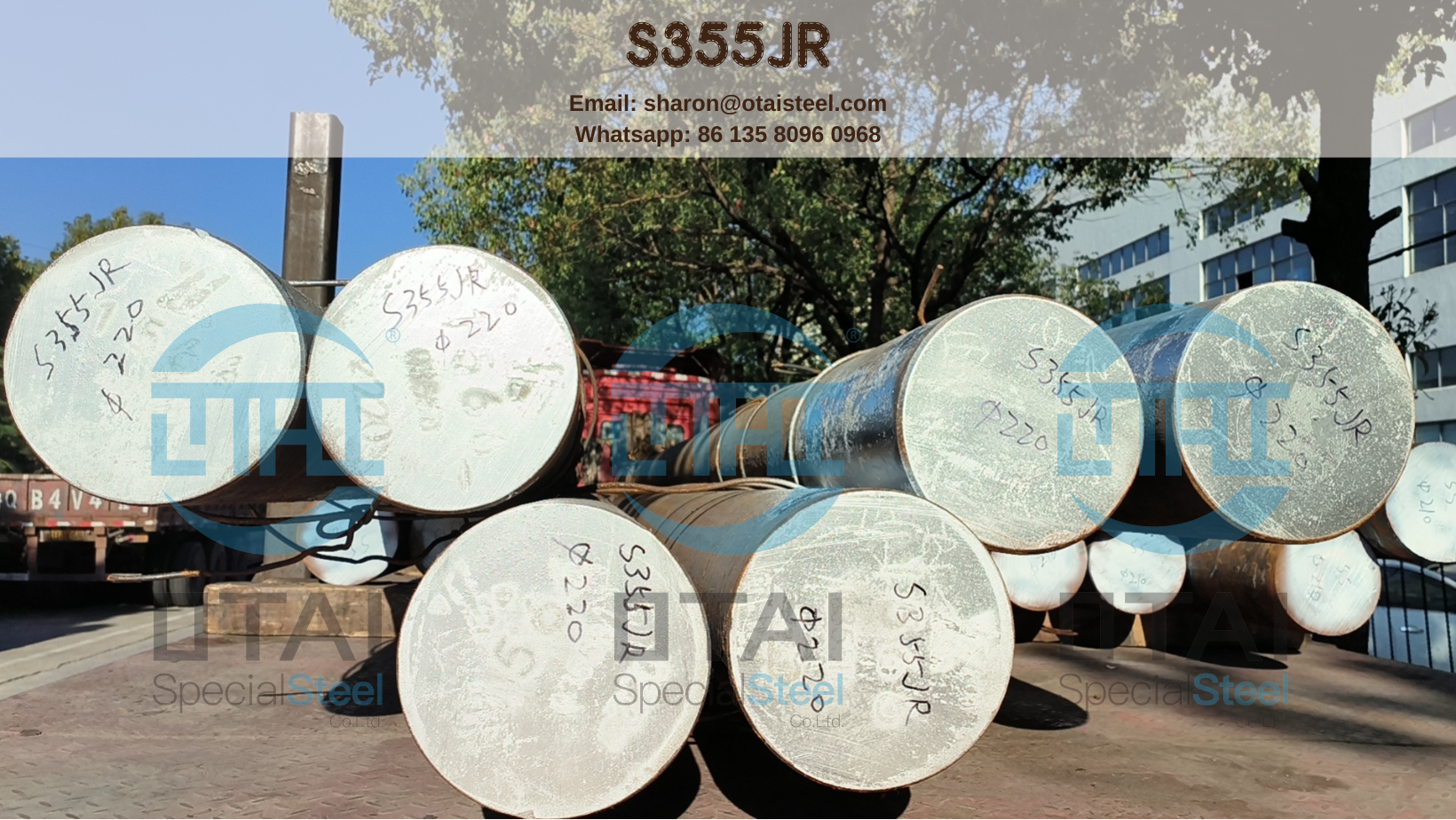