In the realm of steel materials, the name 1.2085 steel resonates with excellence, offering a versatile array of applications across various industries. If you’ve been searching for insights into this remarkable steel type, you’re in the right place. In this comprehensive guide, we will delve deep into the world of 1.2085 steel, exploring its properties, applications, and even uncovering its equivalent grades. Let’s embark on this journey together.
Understanding 1.2085 Steel
1.2085 steel, also known as AISI 420F, is a martensitic stainless steel with exceptional corrosion resistance and machinability. Its chemical composition comprises:
- Carbon (C): 0.40-0.50%
- Chromium (Cr): 12.50-14.50%
- Manganese (Mn): 1.00% max
- Phosphorus (P): 0.040% max
- Sulfur (S): 0.15-0.35%
- Silicon (Si): 1.00% max
Key Properties
- Corrosion Resistance: 1.2085 steel exhibits excellent resistance to corrosion in various environments, making it a preferred choice in applications exposed to moisture and mild corrosive agents.
- Machinability: This steel’s machinability is outstanding, making it suitable for intricate and precision machining operations.
- Hardness: 1.2085 steel can be hardened to achieve a high level of hardness, making it suitable for applications where wear resistance is crucial.
- Toughness: It possesses good toughness, ensuring it can withstand mechanical stresses and impacts.
Applications of 1.2085 Steel
Now, let’s explore the diverse applications of 1.2085 steel:
- Cutlery and Surgical Instruments: Due to its corrosion resistance and machinability, it is often used for crafting high-quality surgical instruments and cutlery.
- Mold Making: 1.2085 steel’s hardness and wear resistance make it a preferred choice for manufacturing injection molds, extrusion dies, and other precision tools.
- Shafts and Bushings: In the automotive and aerospace industries, this steel is used for producing shafts and bushings, thanks to its excellent machinability and durability.
- Valve Components: It is utilized in the production of valve components for its resistance to corrosion and ability to withstand high-pressure conditions.
1.2085 Steel Equivalent Grades
1.2085 steel belongs to the AISI 400 series of stainless steels. It has several equivalent grades in different international standards. Here are some of them:
- DIN: X33CrS16
- EN: 1.2085
- JIS: SUS420F
- UNS: S42020
These equivalent grades offer similar properties and can often be used interchangeably depending on regional preferences and industry standards.
In conclusion, 1.2085 steel is a remarkable material with a wide range of applications, from cutlery to mold making and beyond. Its exceptional properties, including corrosion resistance, machinability, and hardness, make it a valuable choice for various industries. Moreover, understanding its equivalent grades ensures you can source the right material for your specific needs.
Thank you for exploring the world of 1.2085 steel with us. If you have any further questions or need assistance with your steel material requirements, please don’t hesitate to reach out to us. We’re here to provide expert guidance and solutions tailored to your needs.
Email: sharon@otaisteel.com
Whatsapp: 86 135 8096 0968
I always be here to assist you with any questions or requests you may have.
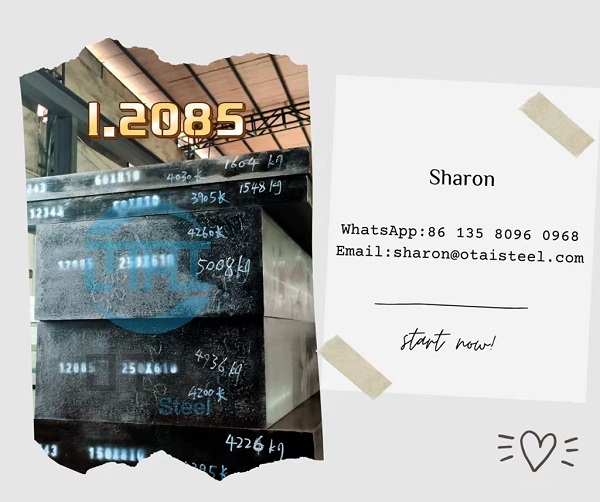